Summary and Features
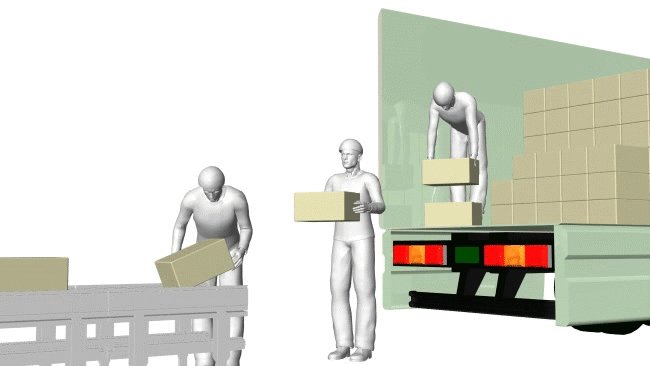
It is a device for manually loading and unloading (labor-saving and worker-saving) loading and unloading of bulk and bulk cargo.
Self-Propelled Mobile Container Work Platform
This loading and unloading system assists manual labor (reducing labor and manhours) when accessing the higher reaches of containers or unloading bulk cargo.
Just 1 or 2 Workers
The Extenor II speeds and improves container devanning, conventionally a labor intensive task requiring many workers.
Let’s solve the devanning problem
Difficult Manual Labor Working Environments
Working inside a cargo container can be arduous, especially in the summer when temperatures inside can exceed 50°C.
It is difficult, dangerous hard work, making it difficult to retain good workers (or find replacements), and aging workforces only exacerbate the problem.
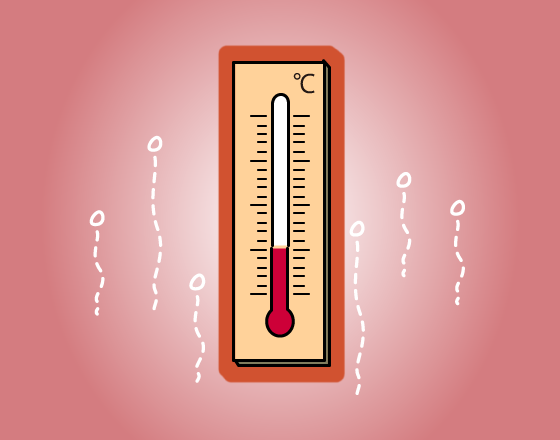
Risk of Injury
Many areas inside cargo containers are high-up and hard to reach, forcing workers into dangerous situations such as standing on top of cargo or underneath potentially falling cargo. Such situations increase the possibility of injury, and lead also to product damage.
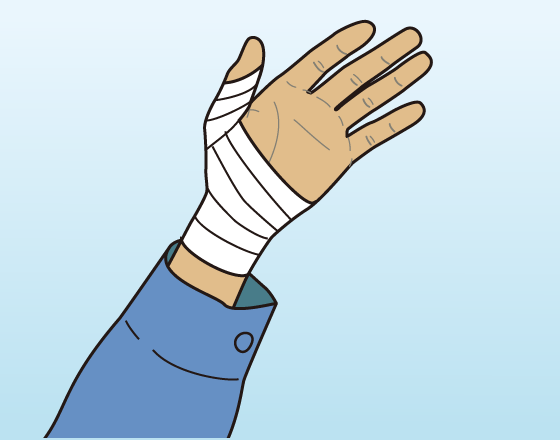
Product Damage
In the container vanning and devanning industry, it has become a pressing problem to find new, more efficient methods that protect worker safety while also eliminating losses incurred when products are damaged or dirtied.
EXTENOR solve these devanning challenges.
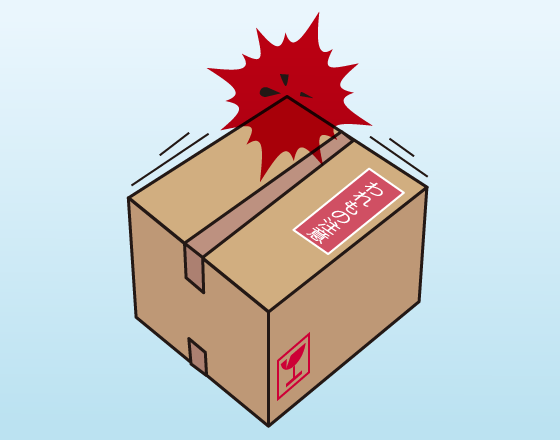
Examples of Application
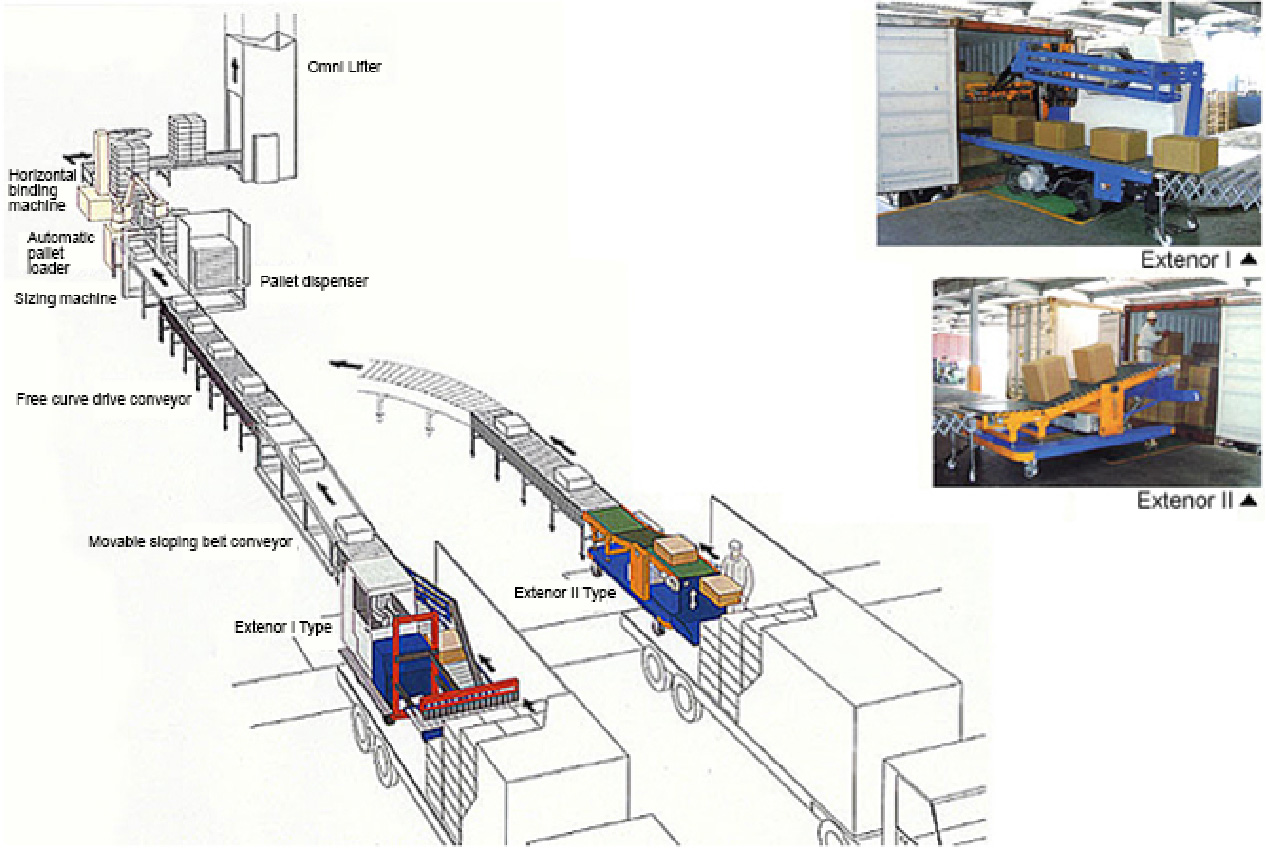
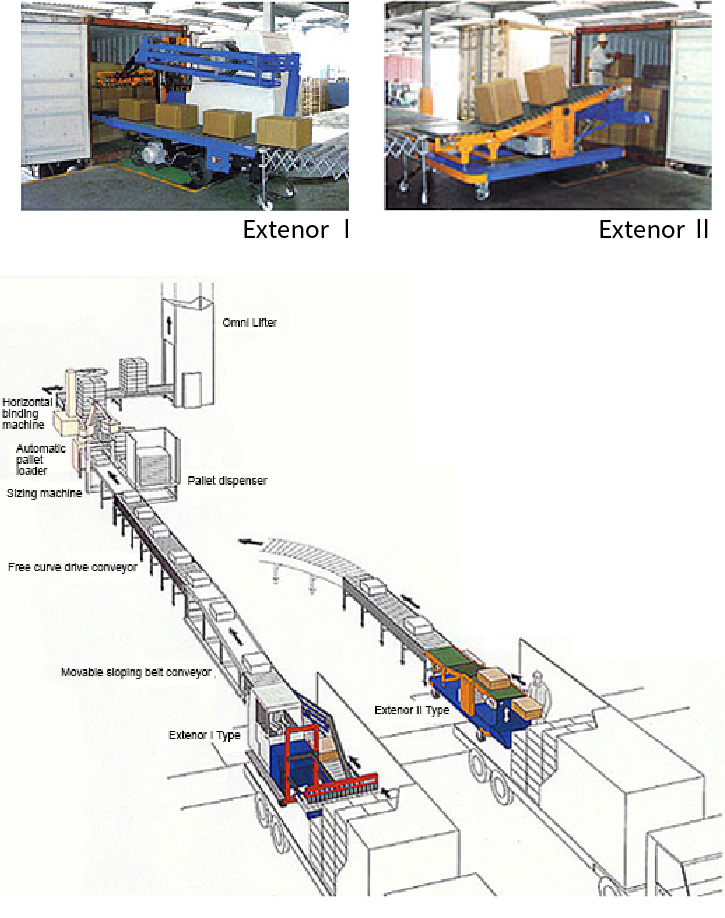
Cases
Basic specifications of EXTENOR Ⅱ
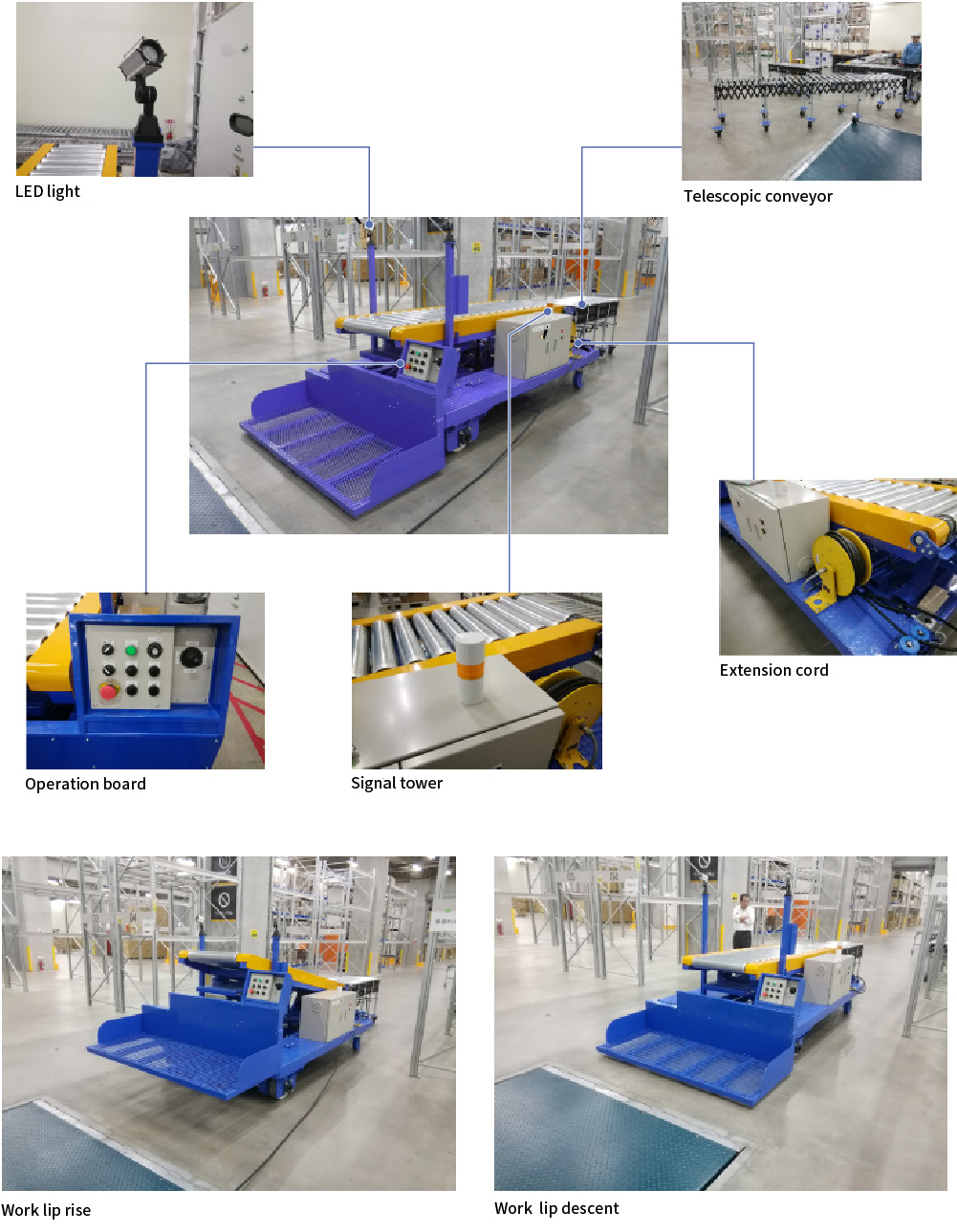
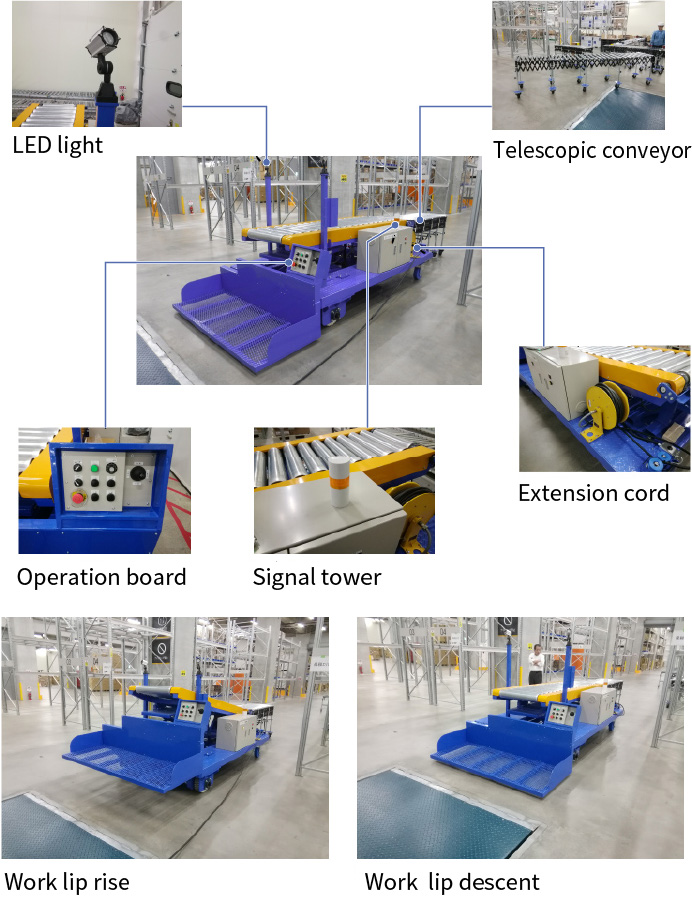
①A certain distribution center
[Before introduction]
- Container 3 times a week
- Additional cost will be incurred if not processed within 2 hours
- There are many cases and it is often not possible to process within 2 hours.
The pallets were placed in a container, and two or three workers palletized the case because it could not be attached to the pallet, and when it was finished loading, it was taken out by a forklift.
It is taken out and reloaded for each product and stored.
[After introduction]
- Reducing worker fatigue
- Reduced work time
- Improving the efficiency of devanning work
After the introduction, even if the load is high, the workers who perform the devanning work can take it out without difficulty, and the work can be done efficiently.
In addition, the case can be dispensed to the outside of the container by a conveyor, and pallets can be stacked in a wide space, enabling palletizing without reloading.
②A certain distribution center
[Before introduction]
- In midsummer, the temperature inside the container rises above 40 ℃ and workers do not settle.
- The palletizing was also done manually and it was difficult because one case was heavy.
- It took more than an hour to dismantle one container.
[After introduction]
- Using EXTENOR Ⅱ, it can be quickly discharged to the outside.
- The combination of palletizing robots has eliminated the heavy labor of palletizing.
Devan → Palletize line schematic diagram
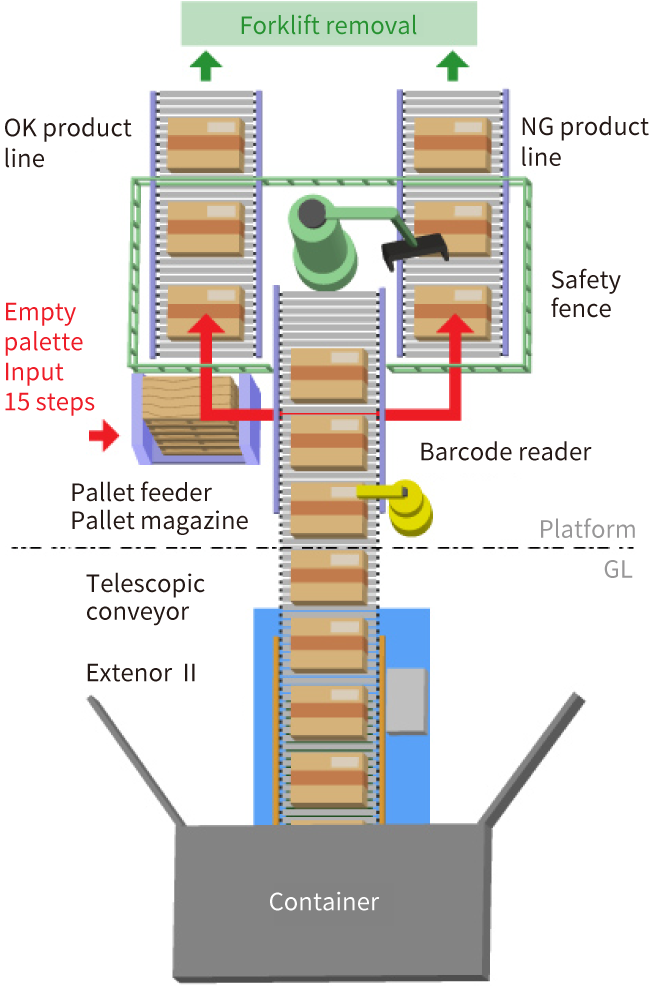
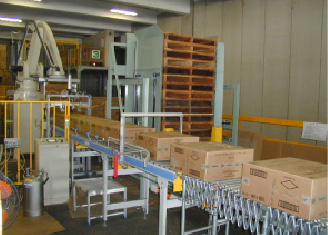
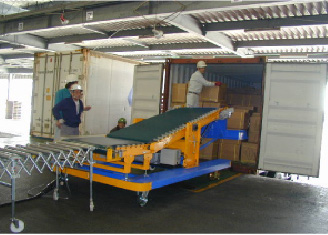
- 1Devan with EXTENOR from the container
- 2Transport by case conveyor
- 3Determine OK / NG with a barcode reader
- 4Supply empty pallets to each line from the pallet feeder
- 5Palletize Robo loads on a pallet
- 6Stock palletized pallets on a storage conveyor
Specifications and Drawings
Outer Dimensions | 1800W×4018L×910H |
---|---|
Work Platform Dimensions | 1800W×800L |
Weight | Approx. 420kg |
Load weight | 50kg |
Work Platform Stroke | 150H~700H |
Climb Gradient | 4° |
Minimum Rotation Radius | 5500mm |
Wheelbase | 1790mm |
Wheels | Powered φ250 Free φ200 |
Options | ・Conveyor full sensor ・”Moving” indicator flasher and buzzer ・200V conveyor power supply 100V drive unit, rechargeable ・Conveyor speed adjustment function (dial or switch) |
* Specifications are subject to change without notice.