Summary and Features
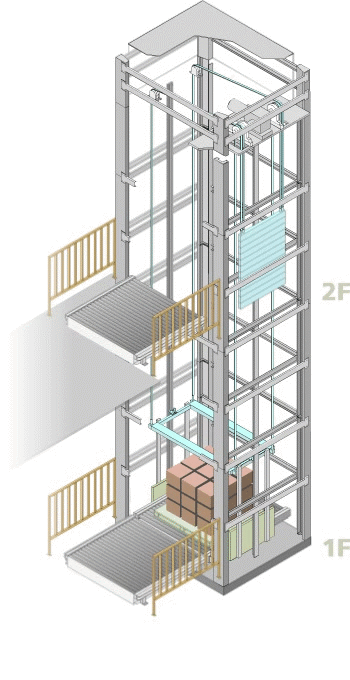
Roller conveyor type, vertical conveyor for pallets.
A mechanical facility
Omni Lifter is recognized by Japan’s Ministry of Land, Infrastructure, and Transport and Ministry of Health & Human Welfare as non-elevator mechanical equipment, and also as Japan’s the first vertical pallet transporter.
Eligible for self-inspection
Since the Omni Lifter is classified as non-elevator mechanical equipment, it is eligible for quarterly self-inspections only instead of costly monthly elevator inspections, which helps reduce running costs.
Smooth acceleration and deceleration
Inverter control smoothes acceleration and deceleration to help mitigate cargo fall worries.
Independent tower frame
Specially designed independent frame offers excellent durability and is easy to install in both new and existing facilities.
Safety first
Safety features based on legal safety regulations offer operators reassurances of safety.
Proven to withstand even major earthquakes
No construction permit required
Unlike elevators, installation of the OMNI LIFTER does not require application for a construction permit.
First in Japan
At the 56th Lift Equipment Performance Standards Committee in April 1975, and by the Labor Standards Inspection Office Manager’s answer issued in April 1976, it was determined that the Omni Lifter is not subject to laws governing elevators, but instead falls under the designation “plant equipment.”
Disaster Prevention (Smokeproof Shutter)
If required for the fire retarding division, smokeproof shutters that operate in synchronization with the smoke detector system are installed according to the examples of construction recognized by the Building Standard Law.
Main Devices
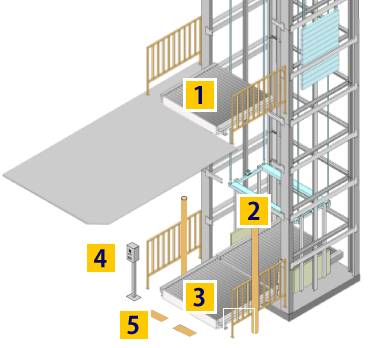
1. Automatic feeding device
A rigid and reliable motor roller. It contains a mechanical strength.
Both pillow blocks and roller chains are located together with a cross-stitch style. It provides a safety to customers for a long time.
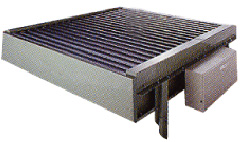
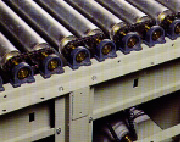
2. Inspection device for
figure of products
By the inspection sensor located on the conveyor, the lifter can detect an over dimension of height and width of products on the pallet, and then the automatic operation will be stopped.
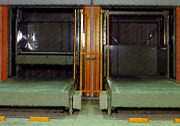
3. Roller sensor
A certain and rigid roller sensor (patent).
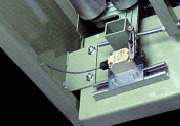
4. Standard control box
(Touch panel)
Full automatic operation with no operator.
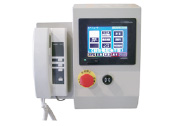
5. Fork stopper
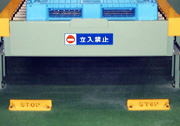
Cases
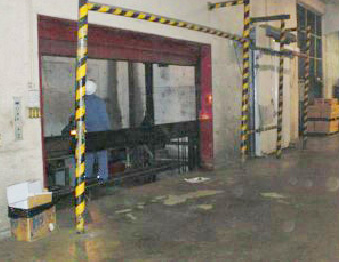
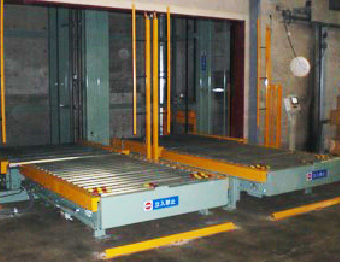
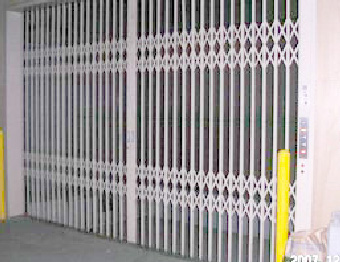
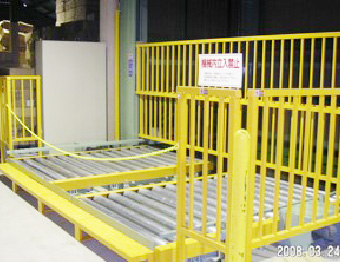
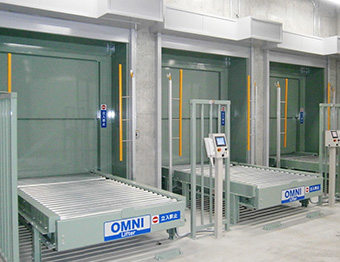
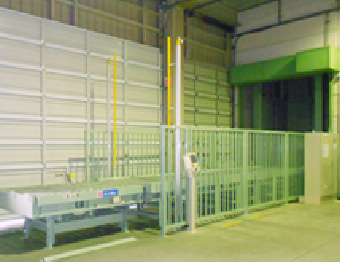
Safety Equipment
-
Abnormal cargo shape detection
(Detects overly wide or high cargos) -
Entrance problem detection
(Monitors the lower portion of the conveyor lift track entrance) -
Ascent problem detection
(Monitors the upper portion of the conveyor lift track entrance) -
Descent problem detection
(Monitors the bottom of descending tables)
Specifications and Drawings
Type | Pallet | Max. Cargo Size | Table | Tower | Aperture | Crossing CV |
Rollers | Feed Mech. L×W |
Feed Mech. H |
Pit Height | Drive Height | Shutter Aperture | |
---|---|---|---|---|---|---|---|---|---|---|---|---|---|
Front×Depth | Front×Depth×Height | TWxTL | W×L | SW×SL | KL | RW | RCL×RCW | RH | PH | OH | Aperture W×HeightH | ||
Model 15 |
1100×1100 | 1200×1200×2000 | 1520×1500 | 2520×1750 | 2820×2050 | 600 | 1300 | 1860×1650 | 600 | 500 | Cargo Height + CV Height + 2000 |
2000 | Cargo Height + CV Height + 500 |
Model 18 |
1300×1300 | 1500×1500×2000 | 1820×1800 | 2820×2050 | 3120×2350 | 600 | 1600 | 2090×1950 | 600 | 500 | 2300 | ||
Model 21 |
1600×1600 | 1800×1800×2000 | 2120×2100 | 3120×2350 | 3420×2650 | 600 | 1900 | 2380×2250 | 600 | 500 | 2600 | ||
Model 24 |
1900×1900 | 2100×2100×2000 | 2420×2400 | 3420×2650 | 3720×2950 | 600 | 2200 | 2630×2550 | 600 | 500 | 2900 |
- * 1Please inquire separately regarding high-speed specifications (70-120 meters/min).
- * 2If adding an automatic door, add 200 mm each to the Tower (L) and Aperture (SL) depth.